i. project background
the company is a global leader in led lighting technology. founded in 1994, the company started from the production of traditional fluorescent lamps and began to transform led lighting in 2010. it is a comprehensive lighting enterprise integrating r&d, production, sales and service. the company is headquartered in xietang industrial zone, shangyu, shaoxing, zhejiang province. it produces hundreds of millions of lighting products such as led and fluorescent lamps. the company's products mainly cover led lamps, panel lamps, commercial lamps and outdoor lamps.
as a product-driven company, the company always puts product development at the forefront, and is able to provide all kinds of lighting products that meet market demand in the first time. as a provider and service provider of lighting solutions, the company is determined to become the world's lighting industry. and front runners. to provide customers with the best lighting application solutions, and to promote the healthy and rapid development of the lighting industry.
the company has its own manufacturing base, more than 40 smt automatic patch production lines produced in japan and korea, 3 independent led automatic lamp production lines, 6 automatic production lines, 25 semi-automatic production lines and matching curing. with integrated equipment, the level of production automation continues to increase. at present, the company has an annual output of 80 million led lamps, led bracket lights, wall lamps, three anti-lights, panel lights and other 20 million, street lamps, tunnel lights, ceiling lights and other 2 million strong production capacity.
at the same time, in order to improve product production efficiency and ensure product quality, the company took the lead in fully implementing the ims intelligent manufacturing system in the led lighting industry, and carried out comprehensive and scientific traceable management of all aspects of the production process. whether it is warehousing, production, acceptance or shipment, the process can effectively control and share information in real time, realizing the "smart manufacturing" in the true sense.
2. customer needs
what problems did the customer encounter:
1. the material carrying method is varied; the tooling return line is too long and the flexibility is poor; the production line is more traditional; the space utilization rate is not high;
2. the flow of people, logistics, and detours lead to a large number of incidental operations without added value. the 5s on-site is poor, and there are too many wip products on site;
3. information transmission depends on information, information records are written, and information is lagging;
4. the material distribution method is a typical one-time large-volume delivery method. once an abnormality occurs in a material, it will cause batch errors.
5. there are a large number of incidental work with no added value during the operation.
lean production line analysis:
1. designing the layout and quantity of lean production lines according to tt;
2. the line body meets the requirements of flexibility and expandability, and can be continuously upgraded to meet the production needs of different products and different processes;
3. the lean production line equipment is modularized, and the lean production line can be assembled freely to improve the efficiency and longevity of the equipment;
4. according to pqpq (order quantity, process path), classify the line body.
lean production line benefits:
the production balance rate has been greatly improved;
the space utilization rate of the site is saved and the floor space is reduced;
optimize the 5s site for easy management and the overall look of the company;
the first mention is flexible, can be quickly switched, and quickly respond to the market;
reduce personnel and achieve provincialization.
3. project improvement
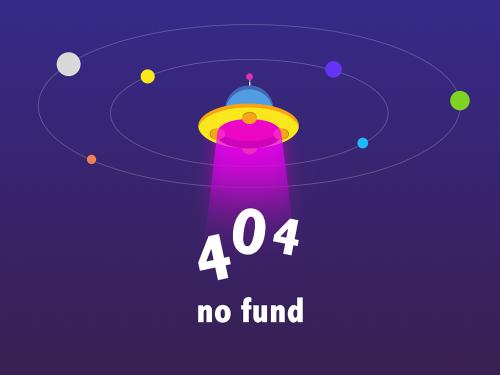
before improvement
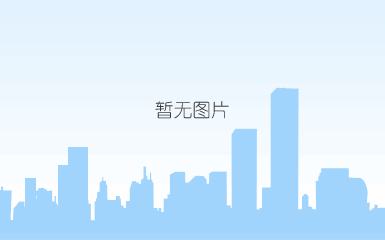
after improvement